Making of a god
Preserving the ancient practice of bronze sculpting in NepalA sculpture workshop run by Mahendra Maharjan in Patan has over 100 specialised craftsmen skilled in sculpting gods. Maharjan is a third-generation artist preserving and practicing the art of bronze sculpting that the city is famous for.
Bronze remains the most favored metal for cast metal sculptures. Maharjan's bronze alloy boasts a high copper content, ranging from 85% to 95%, resulting in a distinctive deep russet tone clearly visible in the pictures.
At his workshop, craftsmen adhere to the traditional lost wax technique, which involves coating a wax model with a mixture of clay, dung, and rice husks. The wax is then melted away, leaving a hollow cast into which molten bronze is poured, giving the sculpture its shape. Skilled craftsmen then enhance the piece further, with one of them using a TIG welder and a rod of the same bronze alloy to weld the seams.
Subsequently, the metal undergoes a thorough cleaning process to remove excess material and fill any pits. The weld lines are carefully sanded down, and carabid-tipped grinders are used to add surface texture, seamlessly blending it with the rest of the sculpture. The process then proceeds to a detailed phase, involving texture carving and precise painting of the eyes and lips. The final touch comes with the addition of precious stones, which enhance the sculpture's appearance, giving it its distinctive and captivating look.
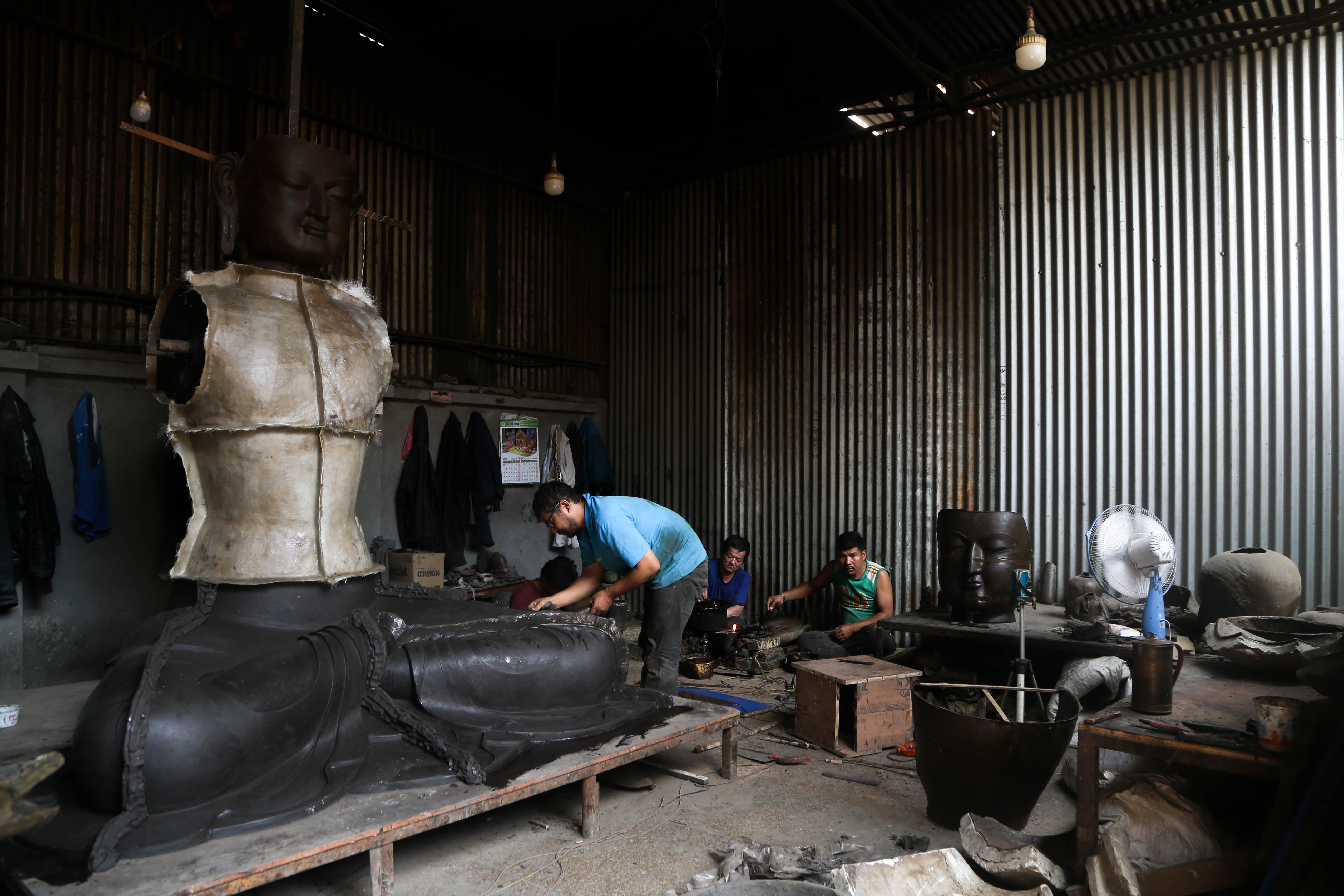
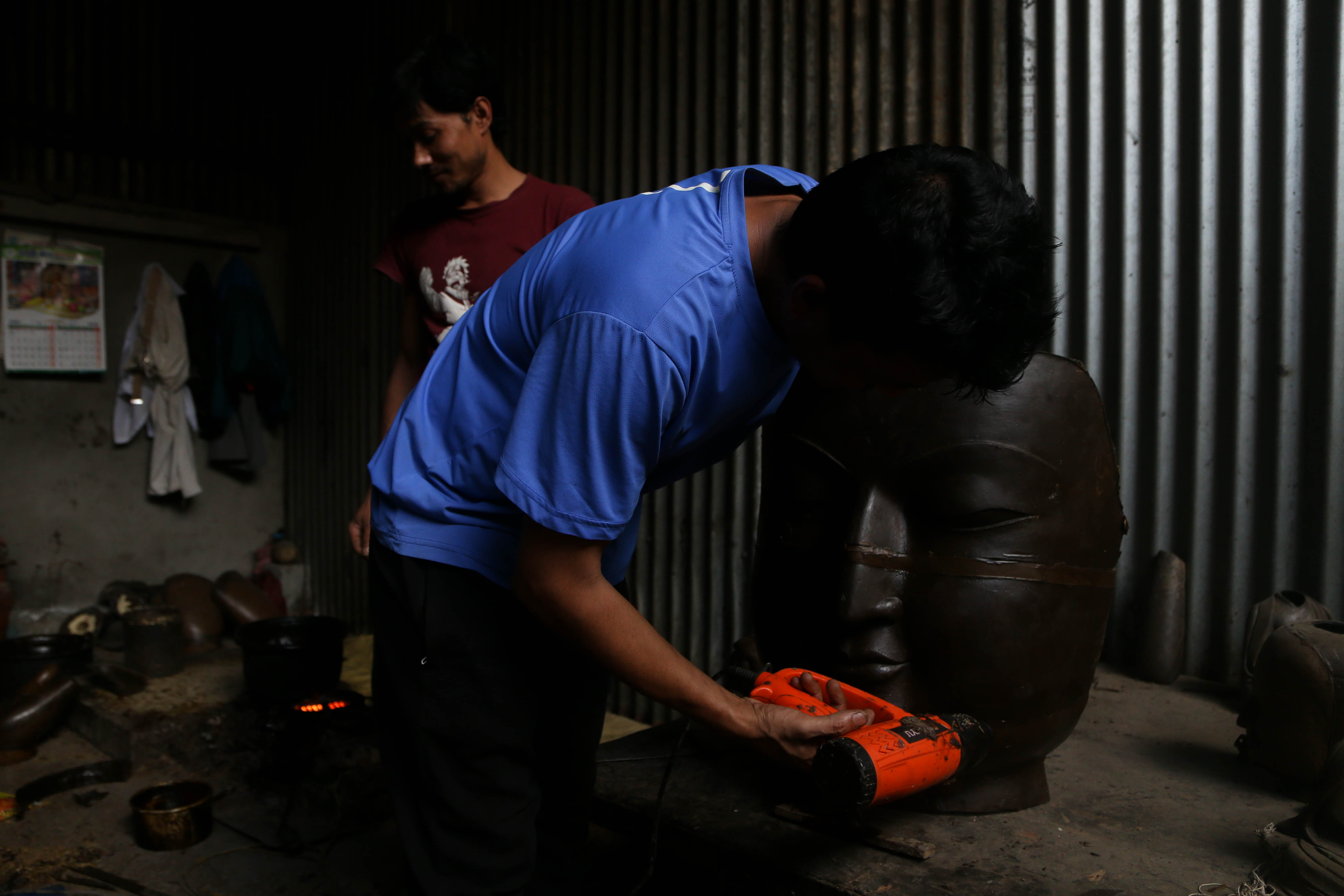
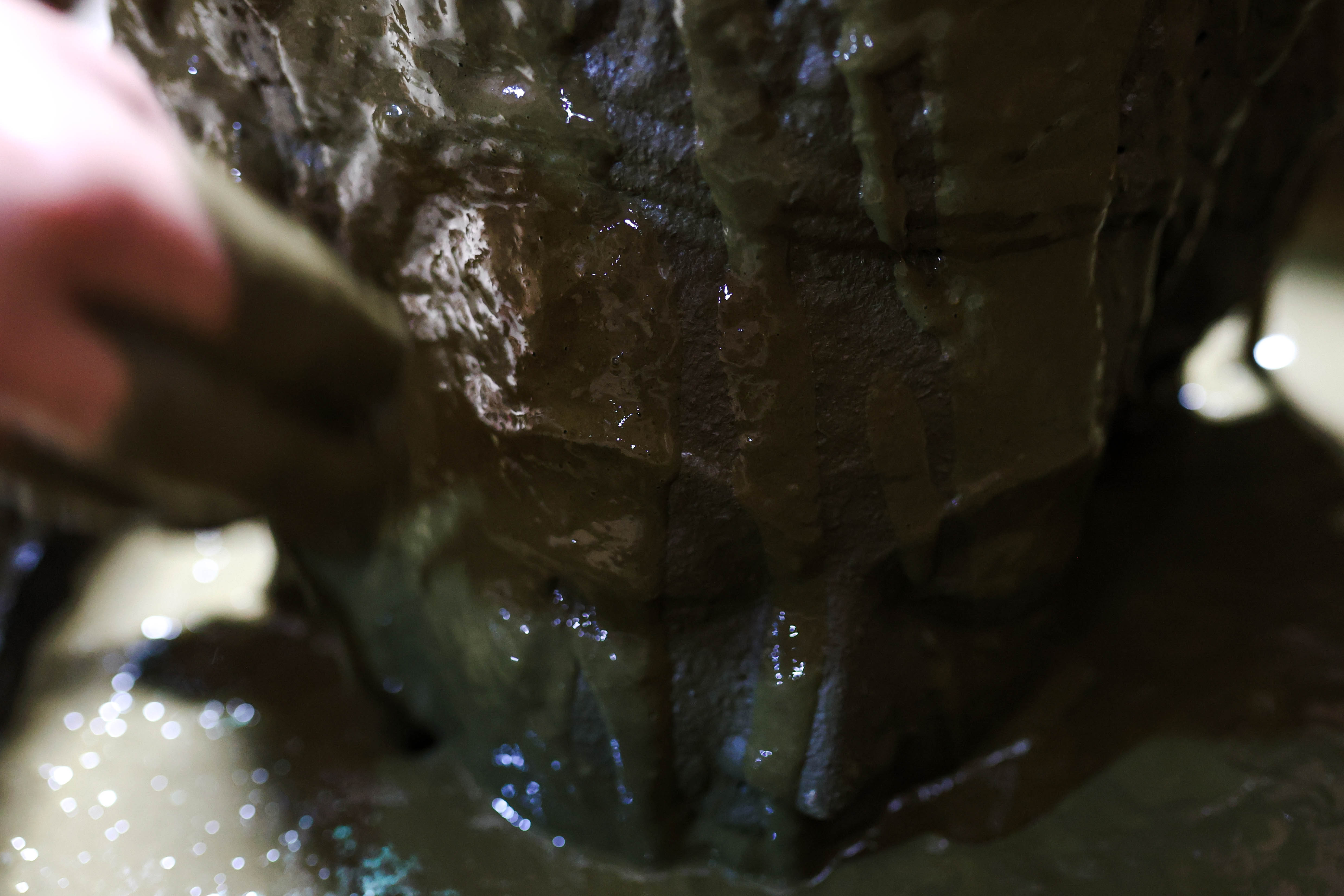
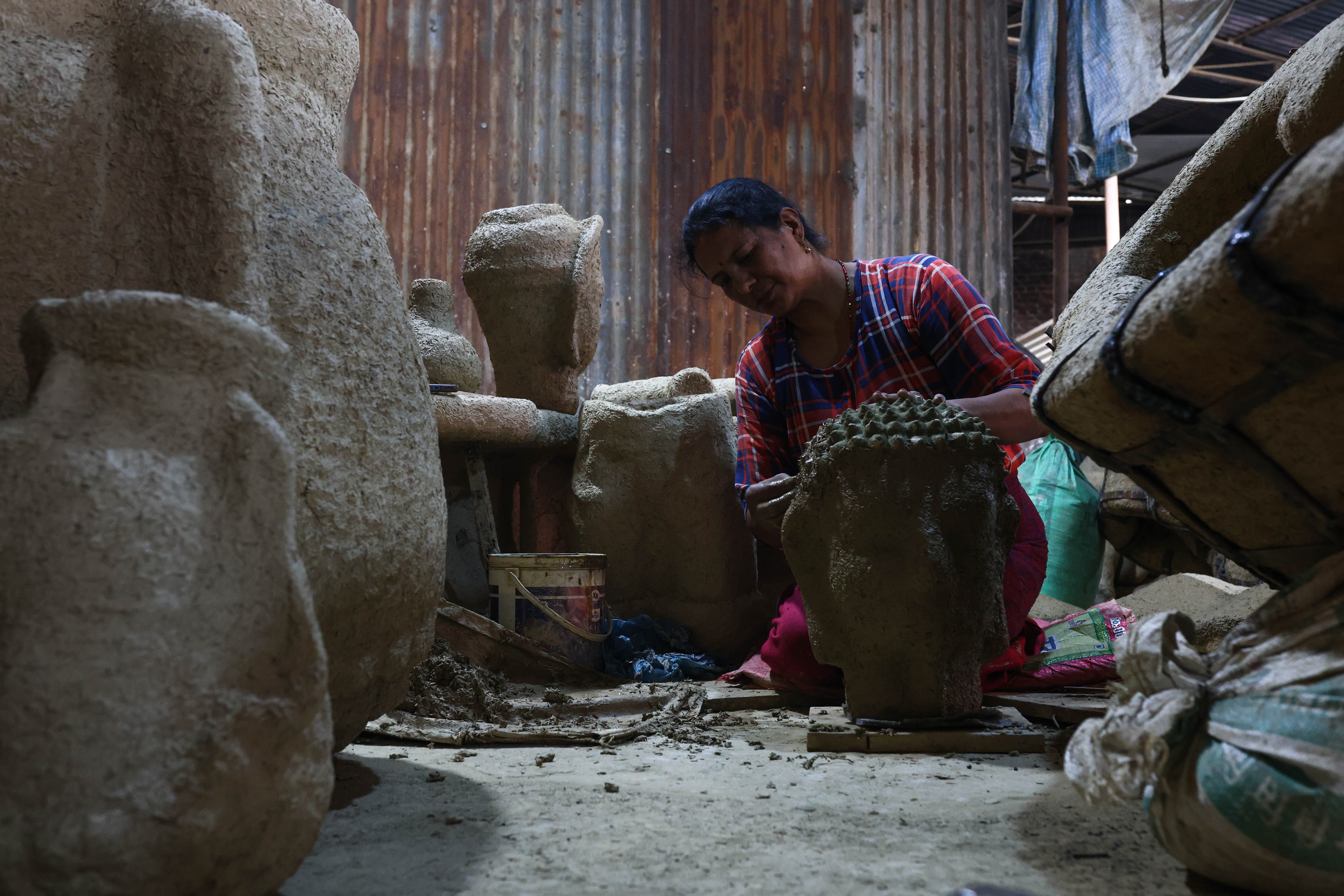
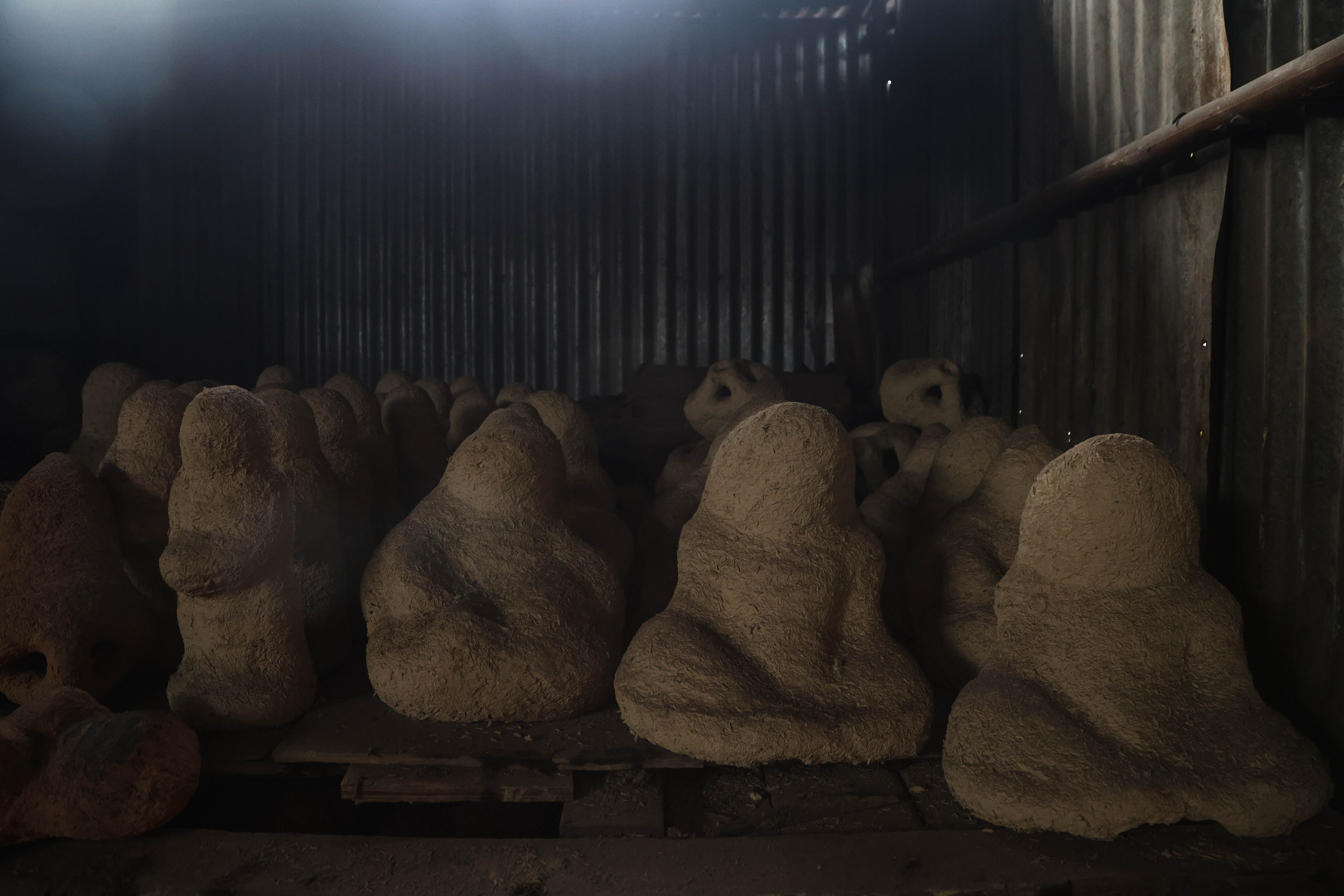
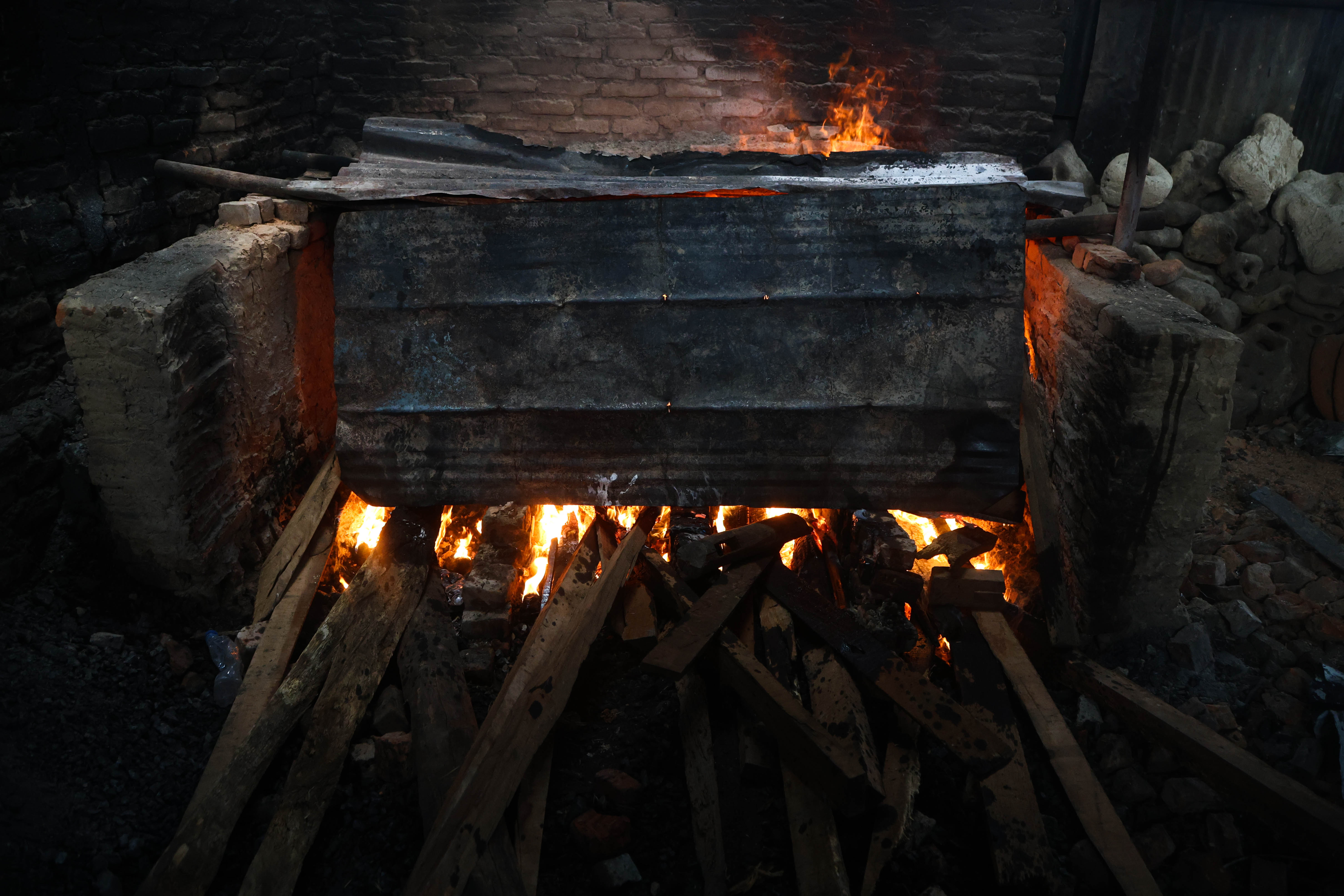
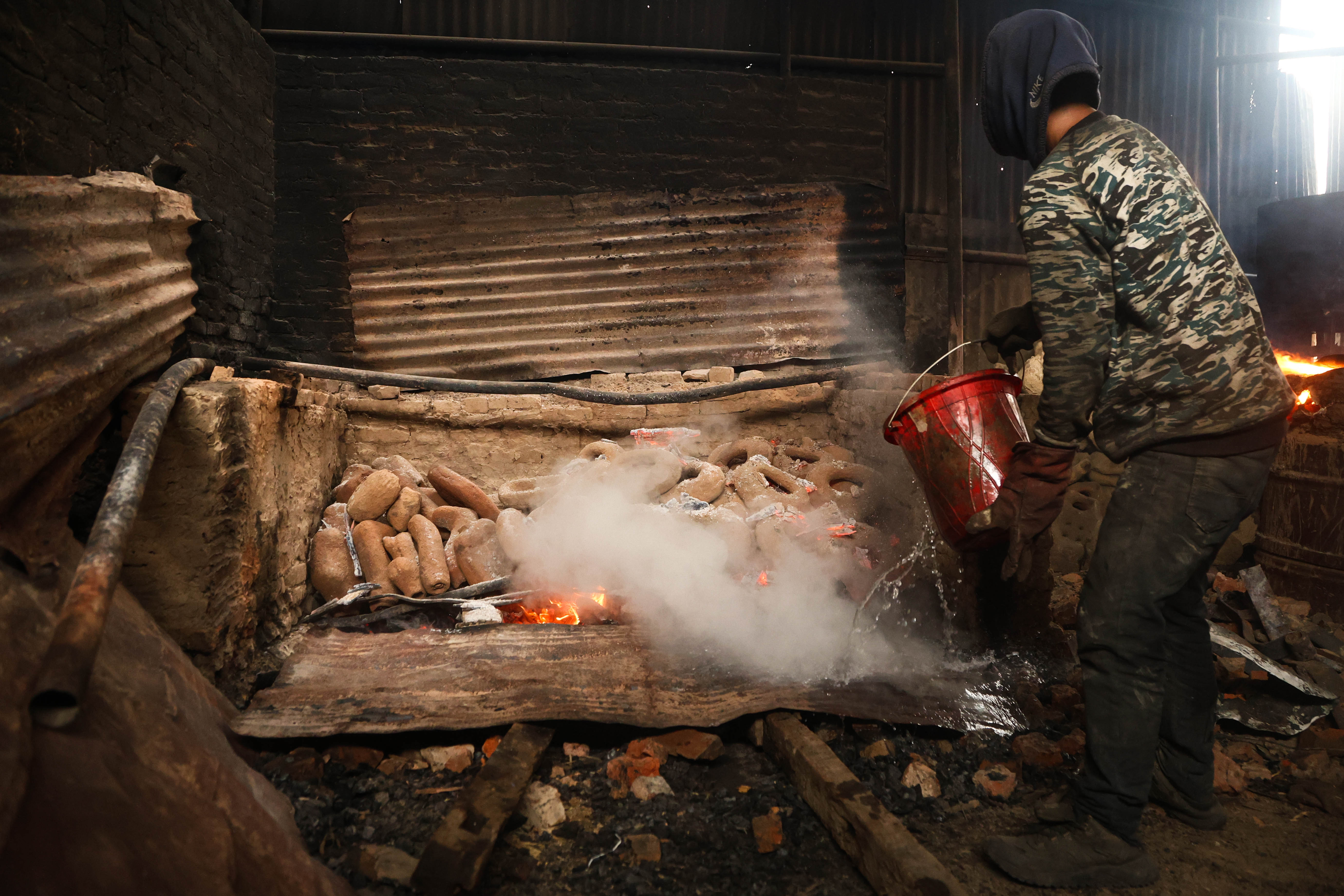
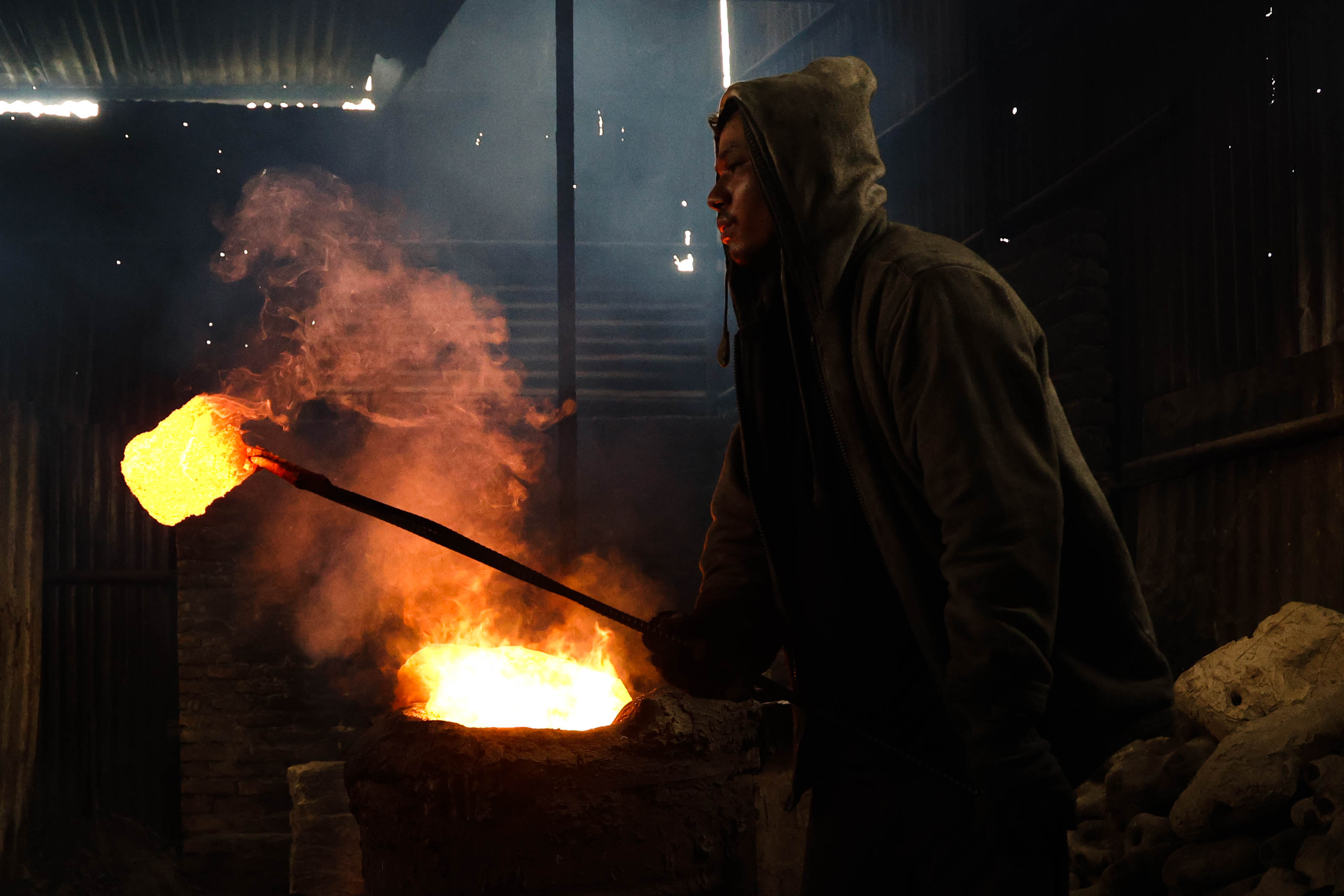
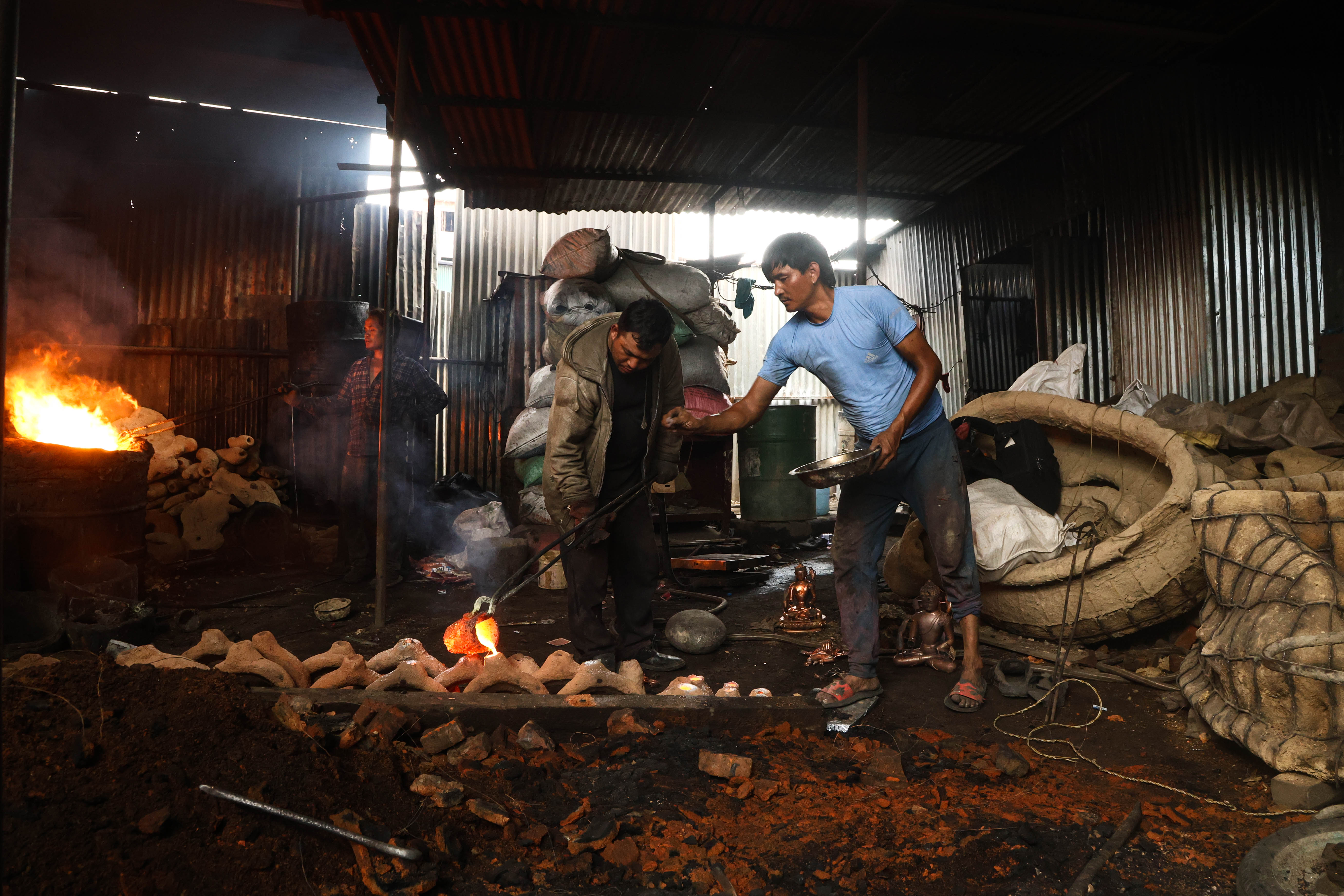
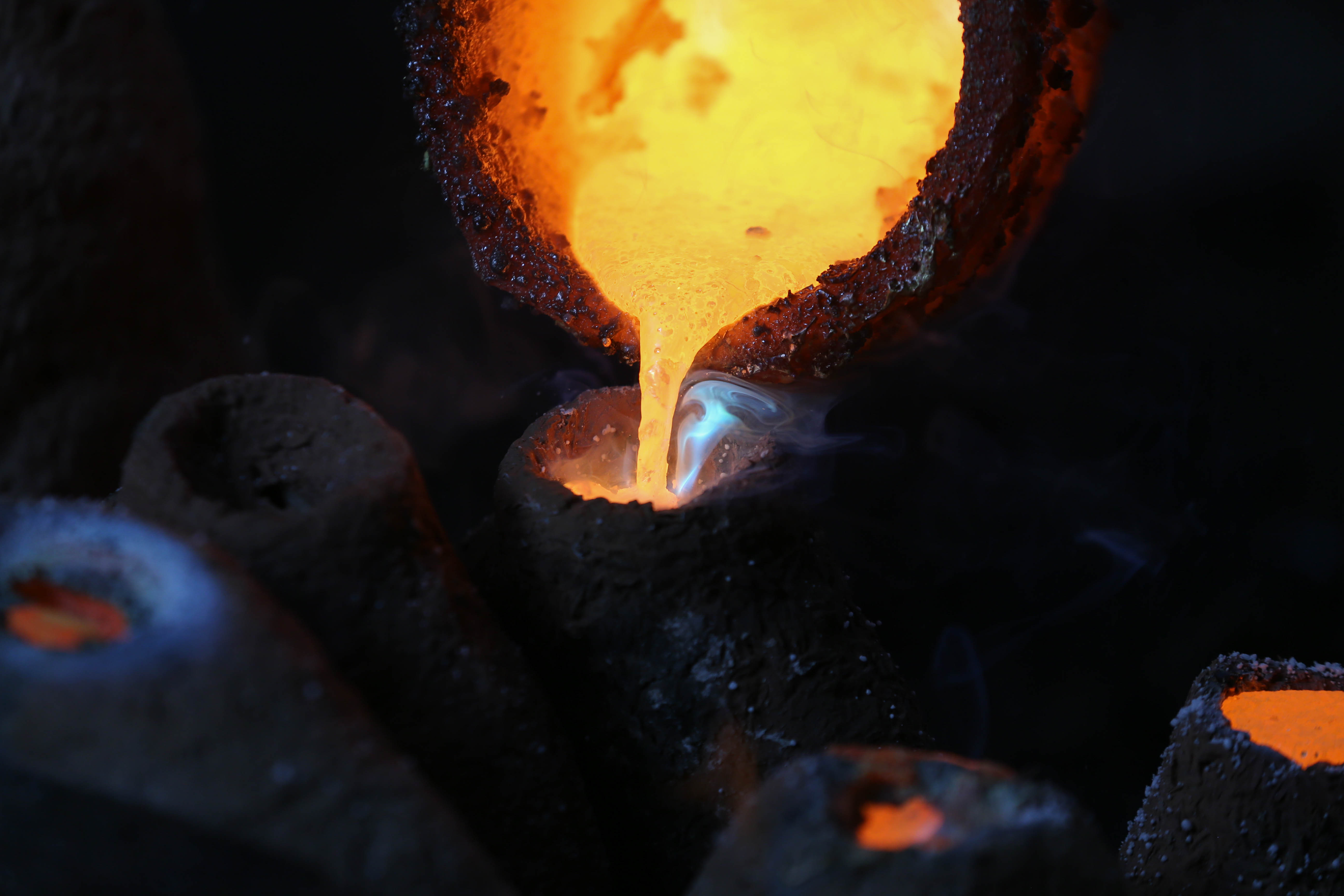
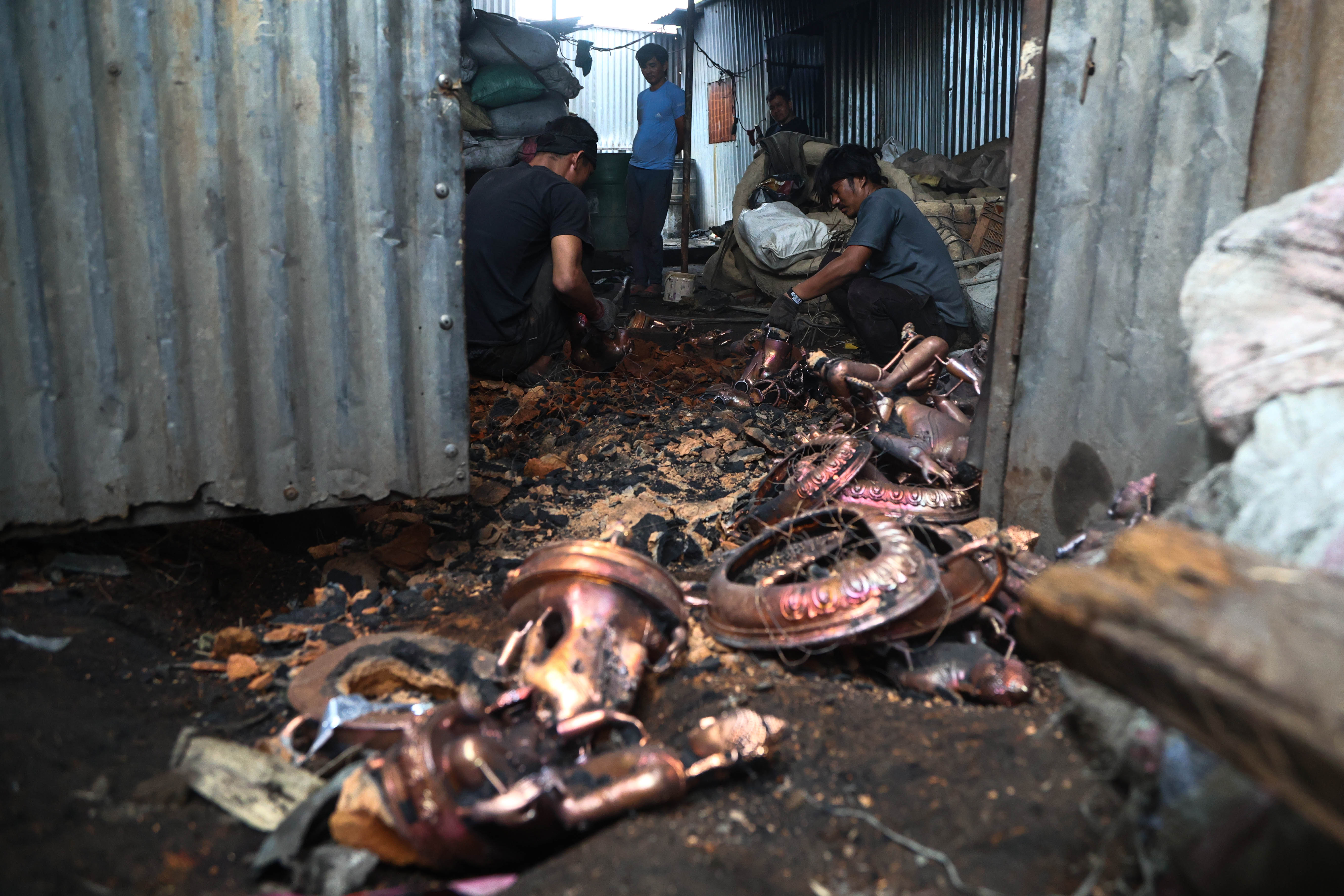
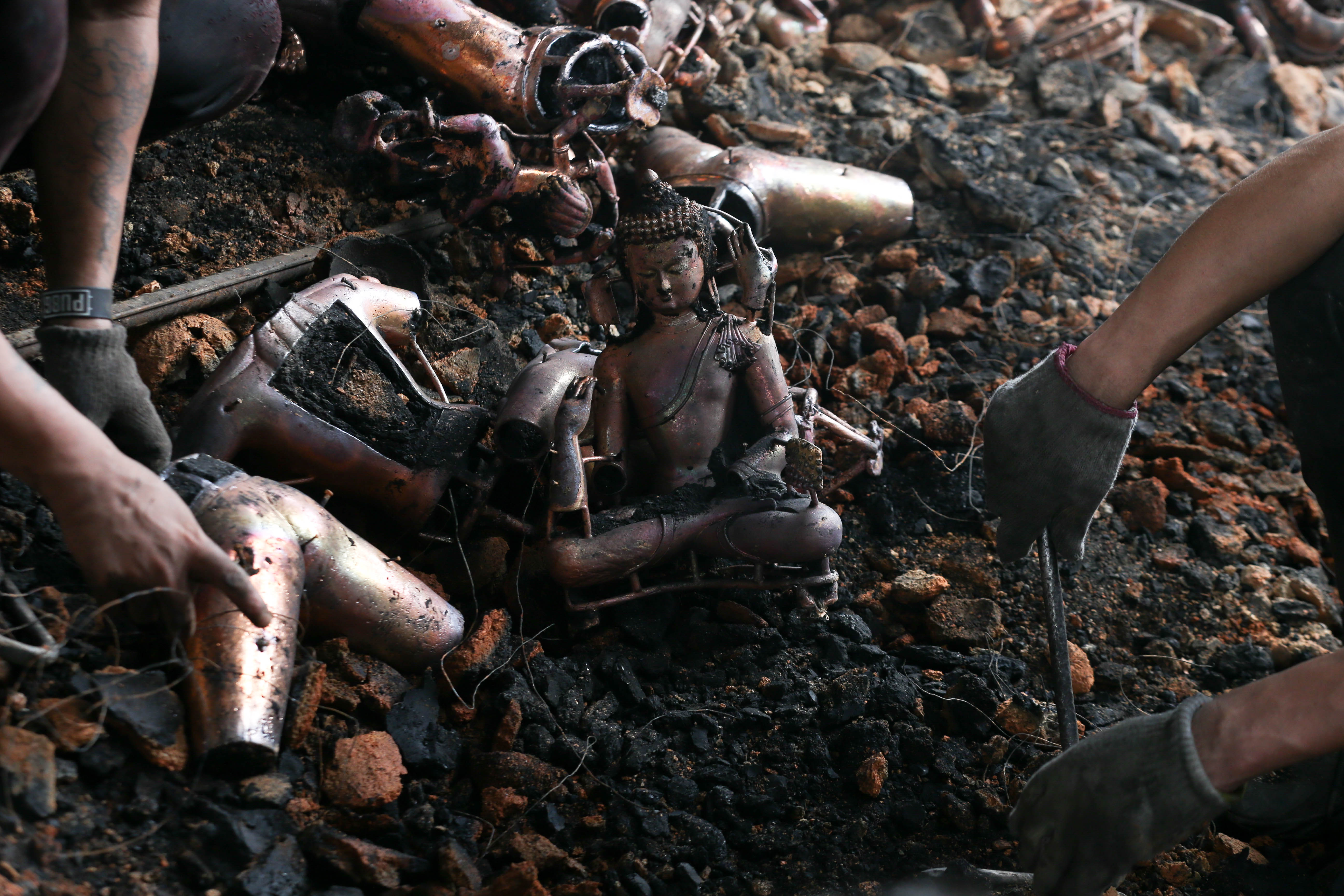
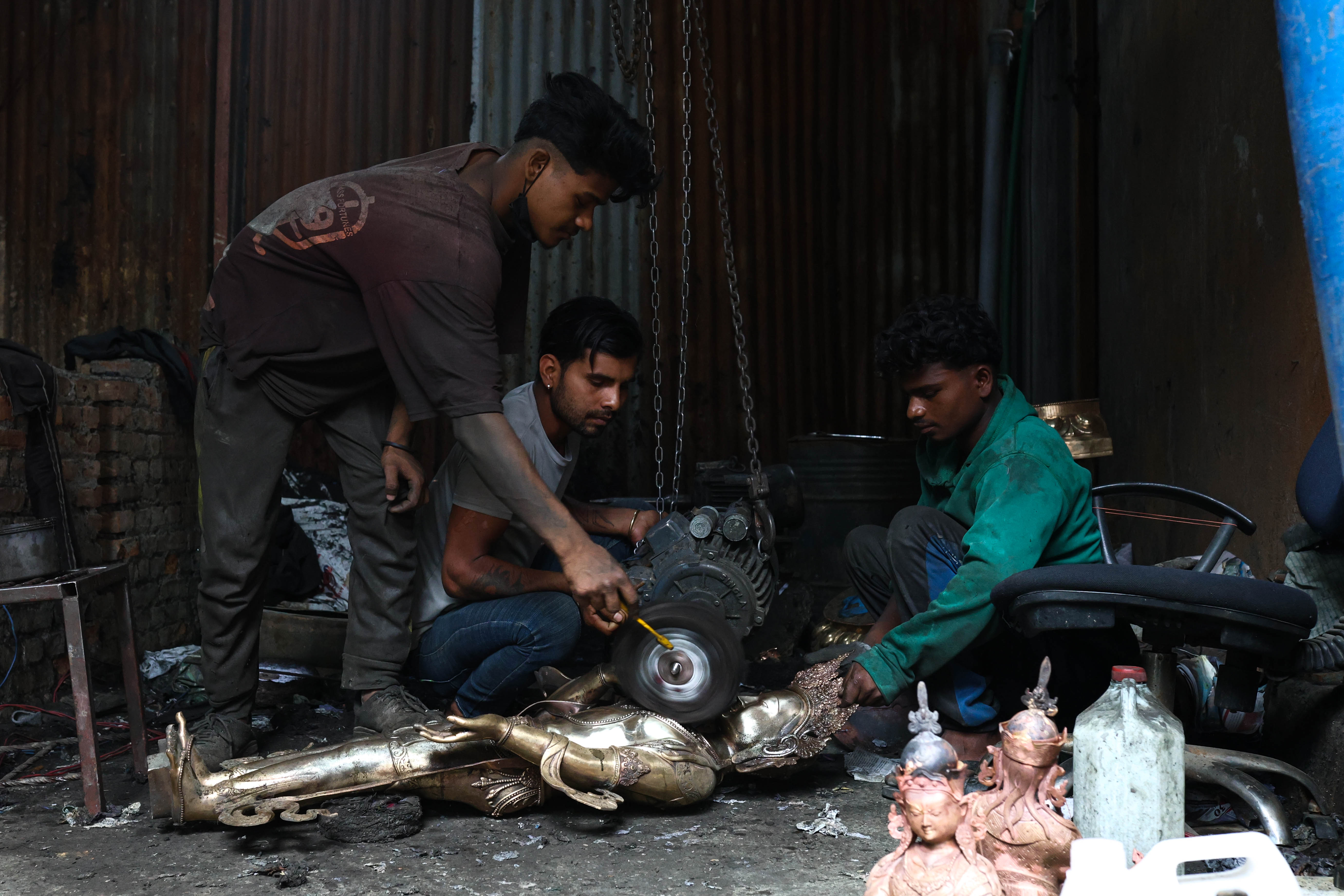
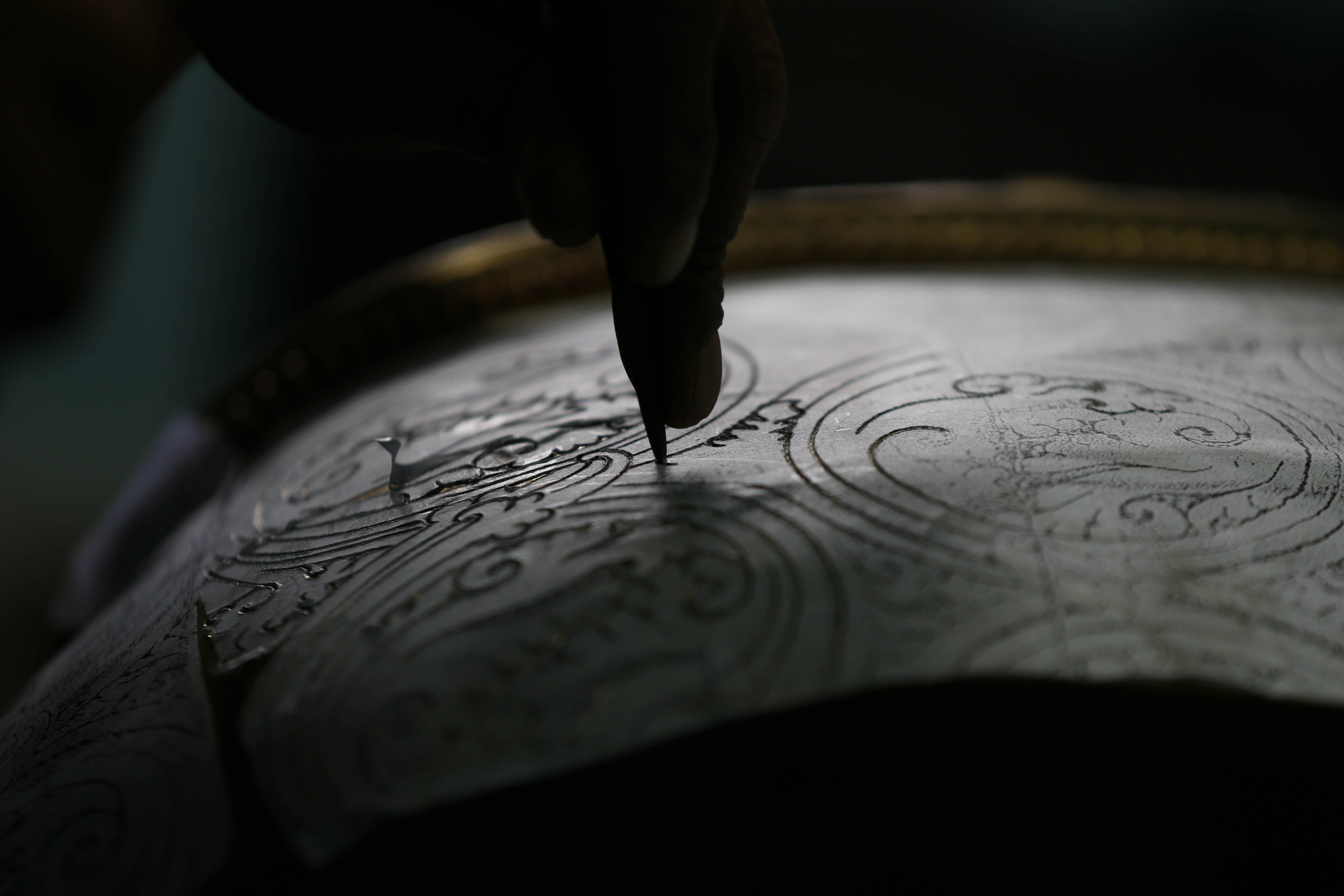
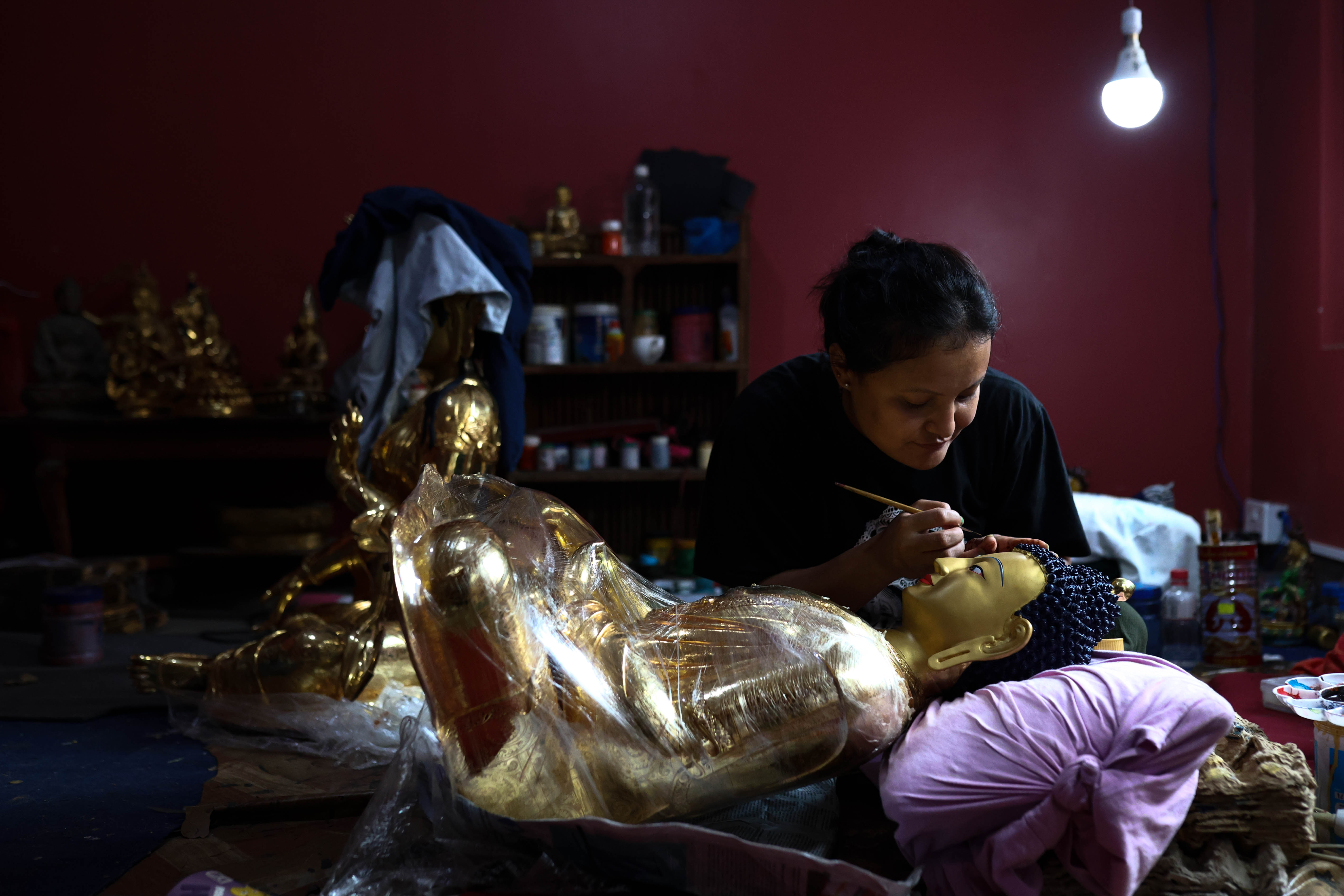
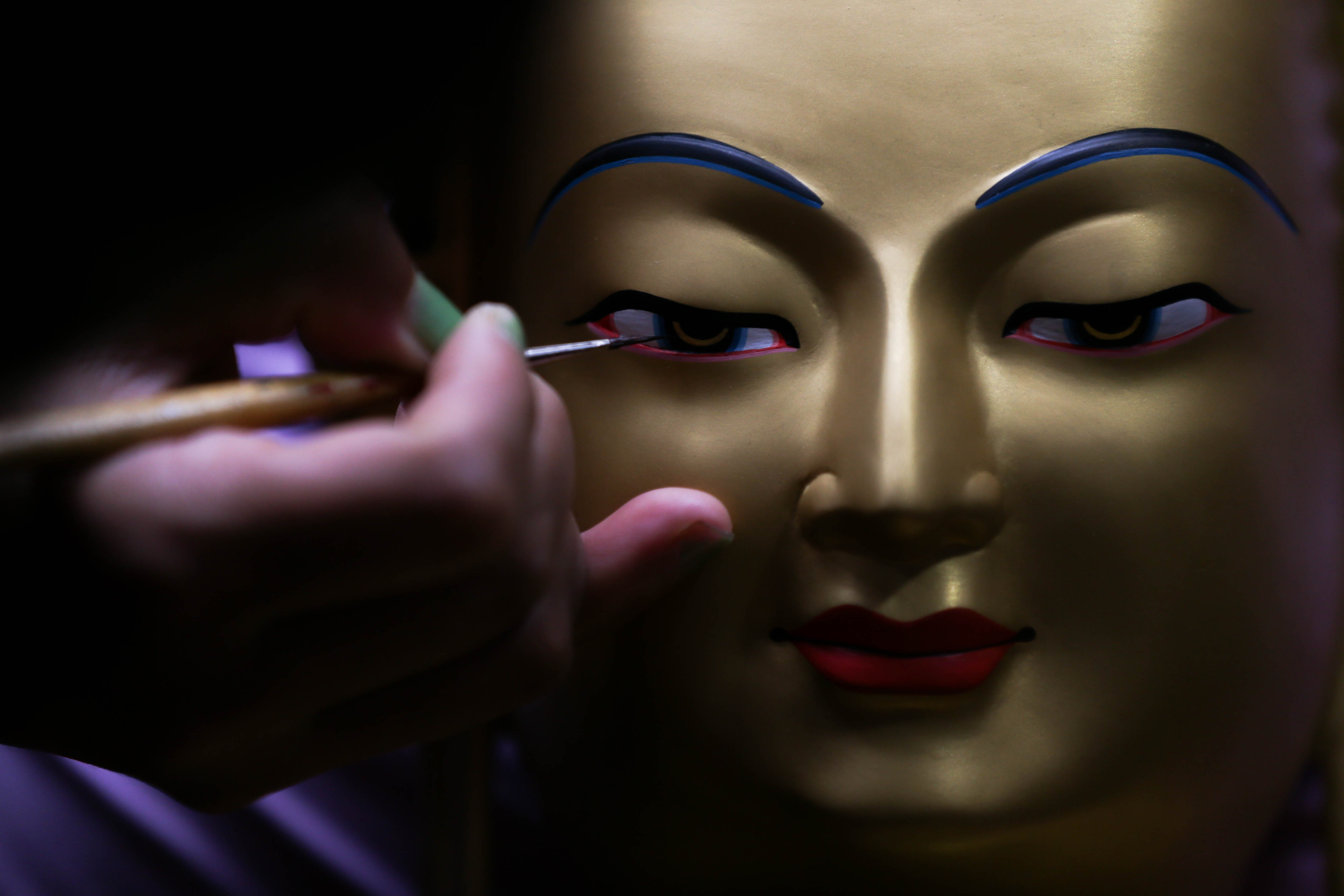
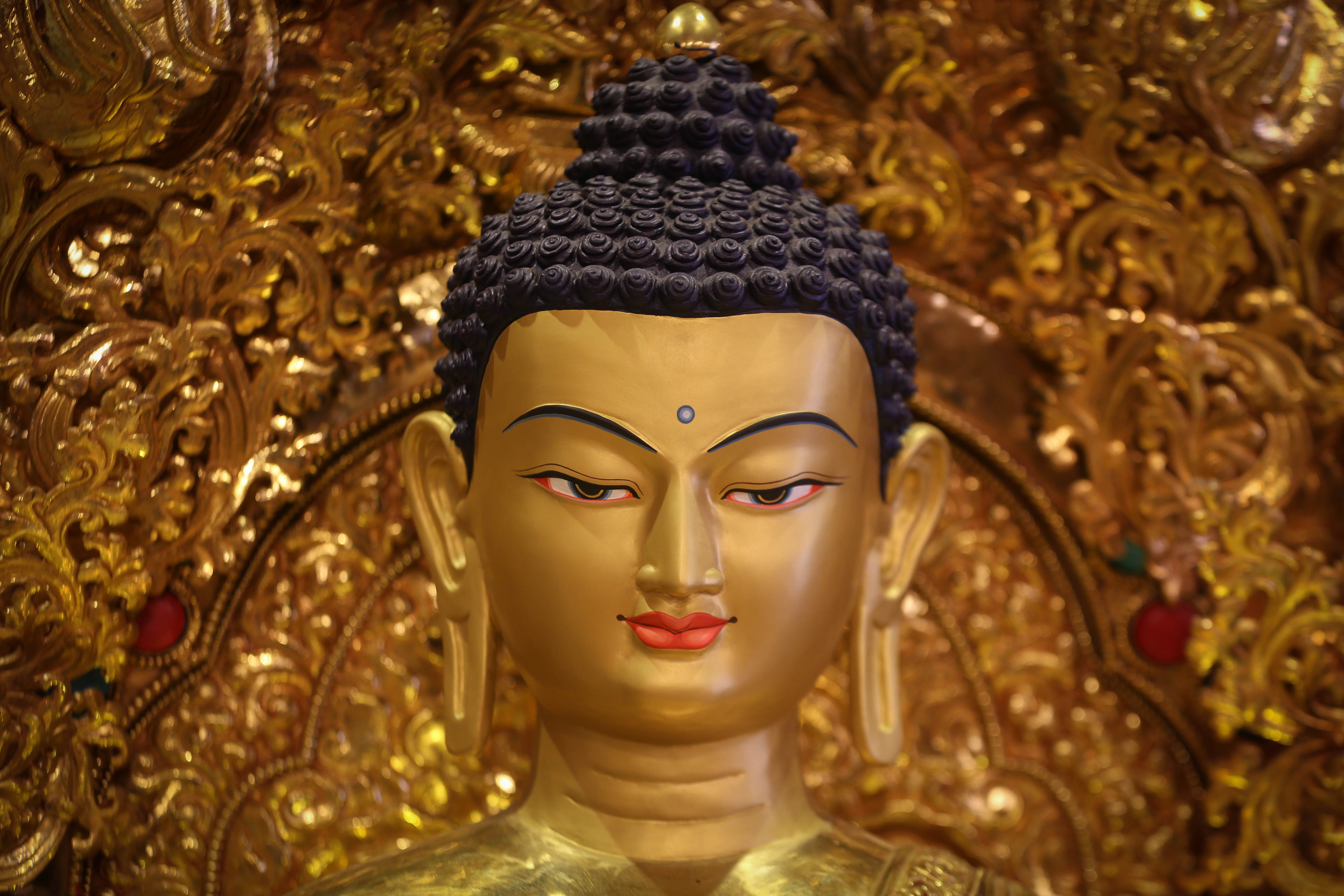
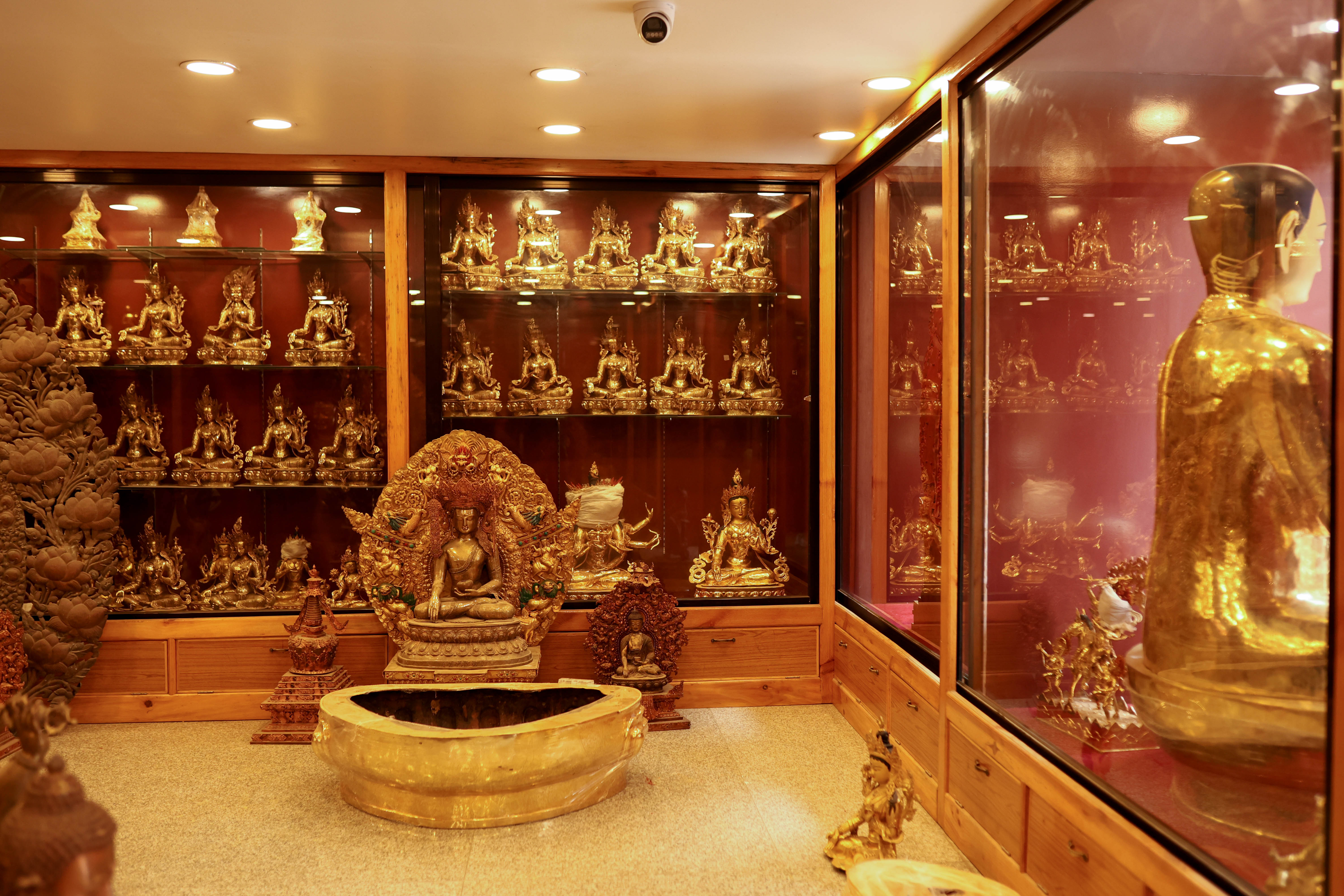